The risks facing Qatar’s mega projects
To prepare for the 2022 World Cup, Qatar will see multiple mega projects in a short time. This will bring challenges such as less planning time, higher costs and scarcity of skilled workers, arguably resulting in poor delivery, writes Ahmed Fouad.
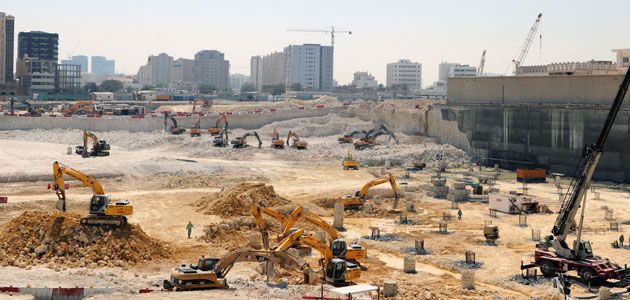
Engineering makes up a significant phase of the proper execution of a construction project. Typically, it starts with a concept design, followed by further design stages before the project is approved for construction (AFC) resulting in shop drawings.
Yet, due to the fast-track nature of the mega projects to meet the time requirements of 2022 World Cup projects, it is expected that these different stages will overlap, creating risks. In many cases, the approval and finalisation of the masterplan is not likely to happen at the time of awarding the projects, which can affect the utilities plant loads, utility lines routing and other interface issues.
Concurrent engineering, scheduling, procurement and construction activities can disrupt the flow of well-coordinated AFC drawings in terms of the mechanical, electrical and plumbing aspects. To avoid such risks, building information modelling must be utilised at early stages of the project as its absence can lead to an enormous number of technical queries. These are likely to cause design changes, which can further affect the quality and delivery schedule of the project.
The procurement procedure is one of the areas with the highest risk probability to cause delays in the delivery of almost all mega projects. One of these risks is that there is no tolerance regarding the preferred vendor lists. Often the client demands material from certain manufacturers and most of them are from European or American factories. This increases both the risk of delayed deliveries and the cost.
“Most of time, the clients demand materials from European or American factories. This increases the risk of delayed deliveries and increases costs.”
Another risk is the delay in final approval for items with long lead times such as switch gears and transformers, etcetera. It is expected that the lead time will increase by 20 percent due to concurrent demand by the various parallel ongoing major projects, in addition to the expected rise in all construction material costs and increase in the delivery time.
One solution is to consolidate all forecasted project requirement schedules by a government organisation to secure the main construction materials such as cement and reinforcement steel, and for contractors to order the material as early as possible and plan for longer delivery times. This can only work if it is supported by flexibility, quick design and material approvals by the clients.
Green buildings
Construction works will be facing new challenges and risks with the focus on sustainability that must be ensured in the heating, ventilation and air-conditioning systems for the stadiums and other aspects of the projects. These trends will lead to the engagement of highly skilled and specialised subcontractors who are new to the region. This will invariably have a cost implication both at the subcontractor and contractor level.
One solution to this could be that the government and the Qatar 2022 Supreme Committee do not schedule projects within the same time frame, especially for the forecasted specialised subcontractors works. This will help reduce the risk of delays and budget overrun. A point must be made to communicate the new lessons learned in fast-track project to all projects which are underway.
Shortage of skilled manpower is another major risk during the construction phase of a project. The situation can become similar to the shortage that happened before the Asian Games in 2006 and again in 2008 during the construction boom in Qatar. But this time, the proportion of the risk will increase due to other factors such as the shortage of efficient workforce on the back of immigration policies which impose restrictions for demographic balancing purposes.
There are other risks at the interface level, especially with government organisations, such as timely issuance of work permit for excavation and construction from Baladiya, final design approval from civil defence, and handover for the fire detection and fighting systems, and approval from Kahramaa for power and utilities supply. These approvals take a long time and with the sheer amount of projects, are expected to take longer, which the country cannot afford.
Like this story? Share it.
-
Q reader
-
Rayan
-
-
pragmaticdr